تقول مجموعة من الباحثين في معهد سكول وفو للعلوم والتكنولوجيا، أو سكوتيك، إنهم طوروا سبيكة جديدة من البرونز والصلب باستخدام التصنيع الإضافي. لقد تحولوا إلى ترسيب الليزر المباشر لإنتاج أجزاء مختلفة تتكون من هذين المعدنين، لأول مرة في السوق. تم استخدام طريقتين: في الحالة الأولى، تم عمل خليط من المعدنين قبل ترسيب الطبقات؛ في الثانية، ترسبت طبقات من البرونز بالتناوب مع طبقات الفولاذ. وفقًا للباحثين، قد يكون هذا العمل مثيرًا للاهتمام بشكل خاص لصناعة الطيران، خاصة في بناء غرف الاحتراق للطائرات والصواريخ.
ليس من غير المألوف الجمع بين مادتين للاستفادة من أفضل خصائص كل منهما – على سبيل المثال هذا هو الاتجاه الذي تتطور فيه الطباعة ثلاثية الأبعاد المركبة بسرعة. في هذه الحالة بالذات، تم اختيار الاثنين بفضل قدرتهما على تكملة بعضهما البعض. يشتهر البرونز بمقاومته للتآكل، والتوصيل الكهربائي الجيد، ومقاومة التآكل العالية. من ناحية أخرى، الفولاذ مقاوم للكسر والصدمات والتشوه الكهربائي وله صلابة عالية. يعد هذا المشروع الأول من نوعه حيث تم إنشاء سبيكة من البرونز والصلب لم تكن معروفة من قبل لعلوم المواد. وكل ذلك بفضل التصنيع الإضافي.
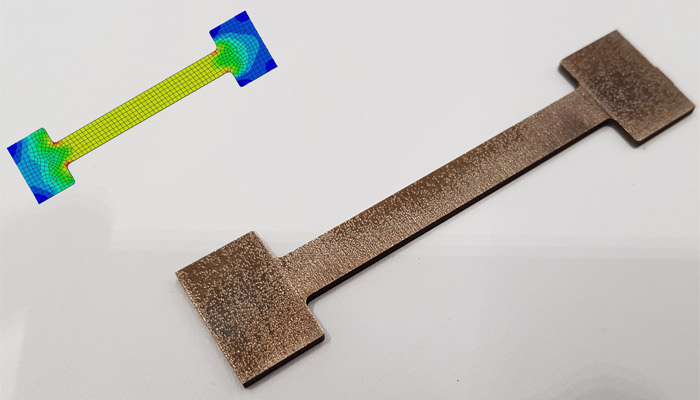
بشكل ملموس، استخدم الباحثون الترسيب المباشر بالليزر (الذي يعمل مثل ترسيب الطاقة الموجهة) لتطوير مشروعهم. أولاً، كان عليهم إنشاء سبيكة متجانسة تقريبًا عن طريق خلط المادتين بطريقة موحدة. ثم تم استخدام هذه السبيكة بواسطة الآلة لتصميم عدة أجزاء اختبار. كانت التقنية الأخرى هي طباعة أجزاء “شطيرة”، أي تتكون من طبقات من البرونز والصلب، يبلغ سمك كل منها 0.25 ملم. أوضح الباحثون أنهم قاموا بتغيير كمية البرونز في كل مرة – من 25 إلى 50٪ – بينما ظل محتوى الفولاذ كما هو.
أوضح البروفيسور إيغور تشايكوفسكي من شركة SkeleTech: ” تعد الطباعة ثلاثية الأبعاد واعدة لتصنيع الأجزاء المركبة، والتي تتمتع بخصائص المادتين المتميزتين التي تشكل المركب. ضع في اعتبارك، على سبيل المثال، أن الفولاذ يقاوم درجات الحرارة المرتفعة الناتجة عن احتراق الوقود في محرك التشغيل. هذا شيء رائع، ولكن بالمقارنة مع البرونز، فإن الفولاذ هو موصل حراري متواضع، لذلك لا يمكن لسائل تبريد المحرك أن يسحب الحرارة منه بشكل فعال لمنع ارتفاع درجة الحرارة والتلف. حسنًا، مع الطباعة ثلاثية الأبعاد، يمكنك في الواقع الحصول على أفضل ما في العالمين من خلال تصنيع غرفة احتراق تتحول بسلاسة من كونها برونزًا من الداخل لتحسين إدارة درجة الحرارة إلى كونها فولاذية من الخارج لتثبيت الهيكل معًا “.
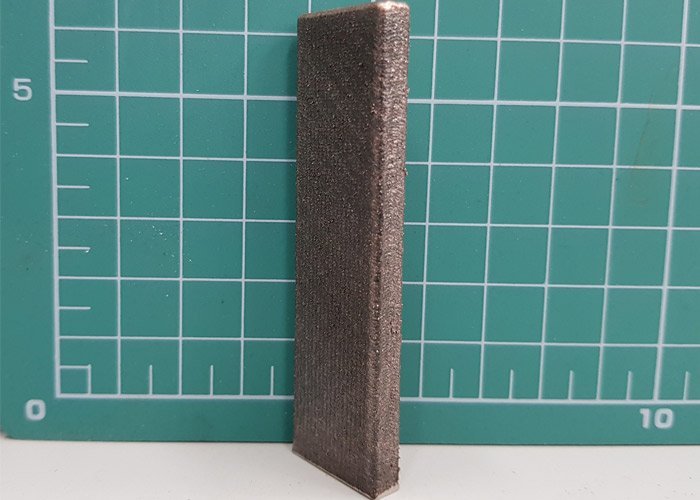
في النهاية، وجدت الدراسة أن المواد اندمجت جيدًا معًا ولم يتم العثور على أي شذوذ. ثم أجرى الباحثون سلسلة من الاختبارات لدراسة الخصائص الهيكلية والميكانيكية للسبيكة الجديدة باستخدام المجهر الإلكتروني البصري والمسح الضوئي. يختتم كوسنانتين ماكرنك، طالب الدكتوراه في السنة الرابعة في Skoltech Materials ، قائلاً: “الآن بعد أن أكدنا أنه يمكن دمج الفولاذ والبرونز في سبيكة ومتوافقة مع الطباعة ثلاثية الأبعاد عبر الترسيب المباشر بالليزر، ونحن نعرف الخصائص الميكانيكية للمادة الجديدة، يمكننا استكشاف تطبيقاتها الممكنة. بالنظر إلى المستقبل، أود تصنيع واختبار غرفة احتراق من البرونز الفولاذي في Soiltech ، ولكن بعد ذلك، هناك عناصر أخرى ممكنة ويمكن استخدام تركيبات معدنية أخرى. ستكون الخطوة التالية هي إنشاء شفرات التوربينات المصنوعة من سبائك فائقة القوة مع قنوات تبريد مصنوعة من البرونز. يتعلق الأمر كله بدمج مزايا مادتين متميزتين في منتج واحد غير ملحوم بدون أي لحام أو منعطفات أخرى “.
المصدر: 3dnatives
قد يهمك: